What is FOCUSED IMPROVEMENT?
Focused improvement includes all activities that maximize the overall effectiveness of equipment (OEE), processes and plants through uncompromising elimination of losses and improvement of performance.
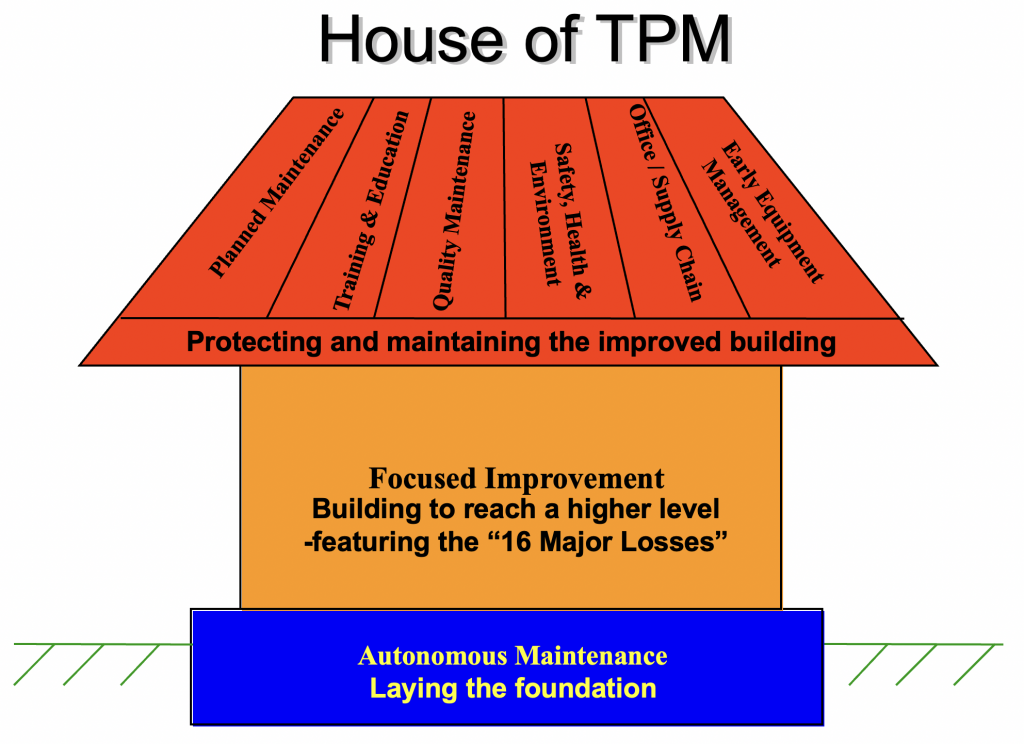
Focused Improvement Funnel
Ideas
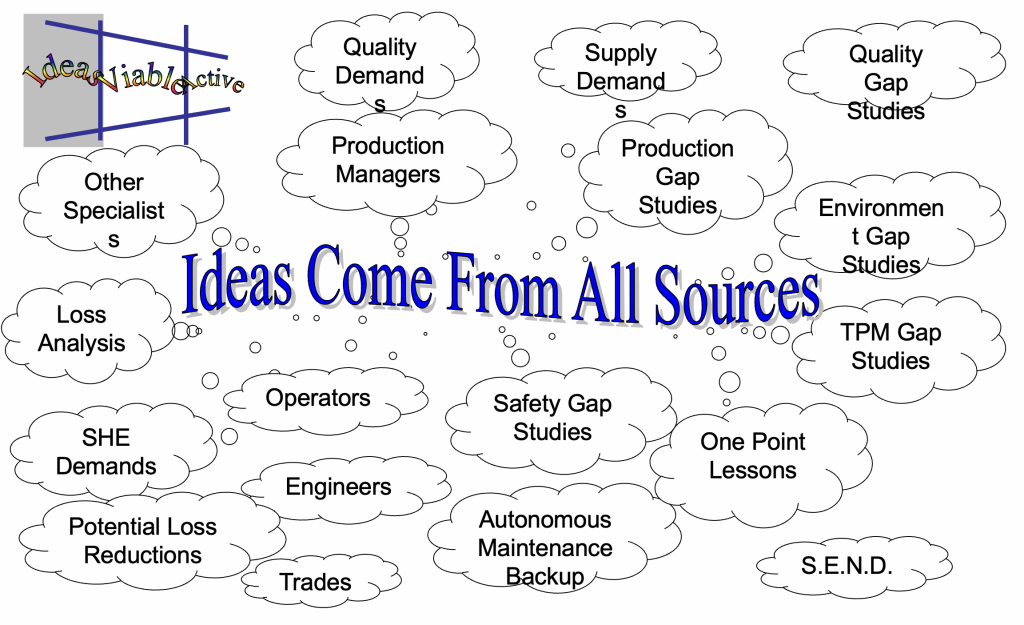
Viable
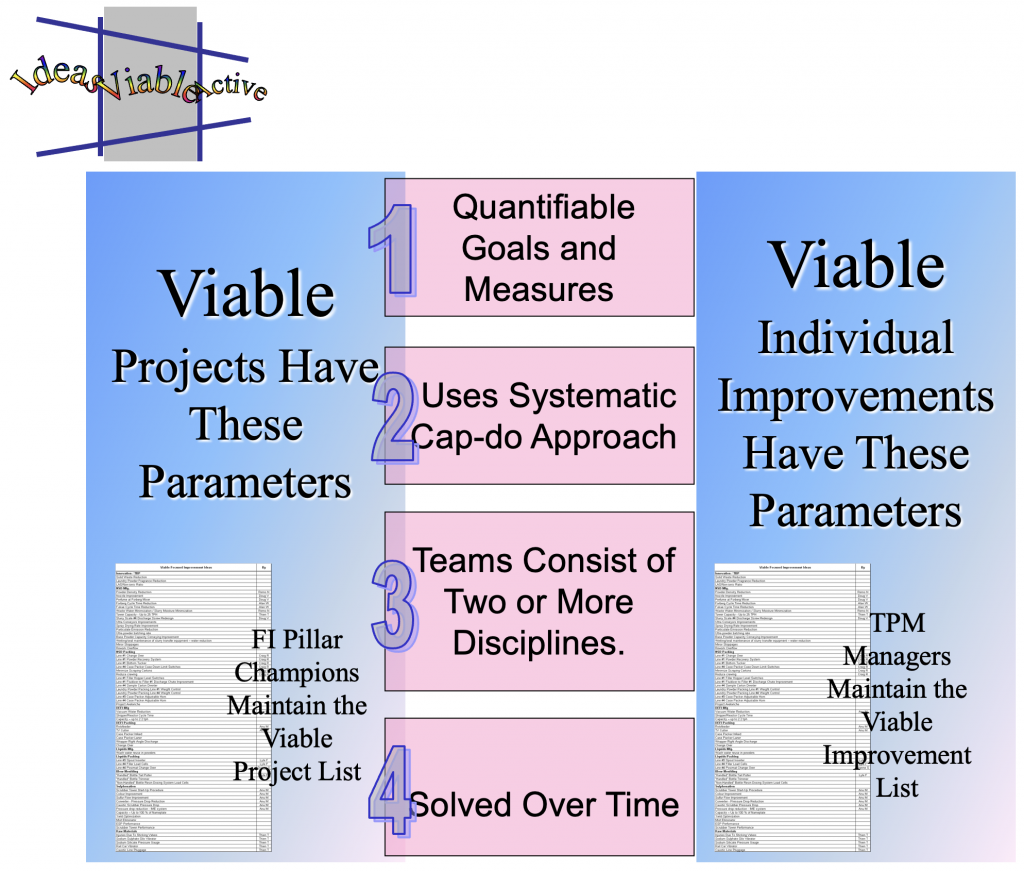
Focused Improvement Methodology
- Select a Topic
- Select and register a topic.
- Form a team.
- Plan activities.
- Understand Situation
- Identify bottlenecks, losses, failures and/or defects.
- Set targets for improvement.
- Expose and Eliminate Abnormalities
- Expose all abnormalities.
- Eliminate deterioration and correct minor flaws.
- Establish basic equipment conditions.
- Analyze Causes
- Analyze losses.
- Apply analytical techniques to determine the root cause.
- Plan Improvement
- Draft improvement proposals.
- Compare the cost-effectiveness of proposals.
- Consider all effects of a proposal on total site performance.
- Implement Improvement
- Determine if improvement works.
- Provide instruction on improved equipment or operating methods.
- Check
- Evaluate results over time.
- Check against targets set.
- If not, return to step 3 (analysis) and repeat.
- Consolidate Gains
- Develop and document control and work standards.
- Feed information back to the maintenance prevention program.
- Extend improvement to other unit operations.
Focus Improvement Board Layout
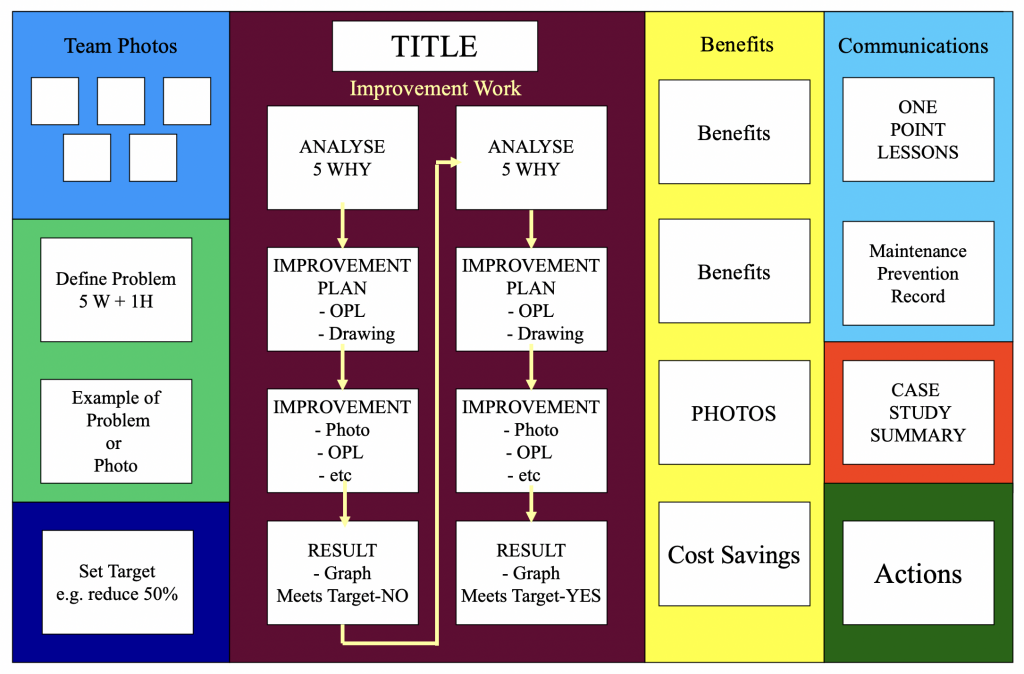
The Focused Improvement Cycle Template can be downloaded here
Other Analytical Techniques for Improvement
Some other analytical methods useful in focused improvement include:
- P-M analysis (phenomena are analyzed in terms of their physical principles)
- Know-why analysis (also called “why-why analysis”)
- Fault-tree analysis (FTA)
- Failure mode and effect analysis (FMEA)
- Industrial Engineering (IE)
- Value analysis (VA)
- Just-in-time production (JIT) or Toyota production system (TPS)
- The original seven QC tools and the seven new QC tools (also called the seven management tools)
How do I possibly know what happened? I wasn’t even here then … last shift/week/hour/ever?