In this article, I will briefly touch on the TPM concept and then describe how I used the elements; what I later learned through a TPS training by Toyota Engineering Corporation (TEC) was actually Equipment Kaizen. Anyway, we made the improvements through a Kaizen Event in 5 days, and it is this process I want to describe. The improvement event increased the OEE from 47% to 70% and introduced many elements from the TPM methodology.
Total Productive Maintenance (TPM)
Total Productive Maintenance (TPM) aims to ensure that our machines are always available when needed, which means they are not down due to breakdowns or other unforeseen issues. The methodology focuses on maintaining the machines on different levels so that the equipment is always maintained and ready to perform at the expected level when needed. The “Total” means that everybody is involved in making sure that the machinery is oiled and well-functioning. This is very different from the usual thinking where the maintenance department alone is responsible for maintaining the machinery and where they often at the morning meetings get accused of not maintaining the equipment – forgetting that yesterday the scheduled maintenance was postponed because we were late on a delivery.
The TPM methodology consists of eight pillars and is based on a foundation of 5S:

1. Focused Improvement: Typically reached through smaller teams or groups of employees working together to incrementally improve the performance of the equipment
2. Autonomous Maintenance: Moving easier and lighter maintenance tasks such as cleaning, lubrification etc. from the maintenance engineers to the operators, freeing maintenance up to do heavier and more complicated maintenance tasks
3. Planned Maintenance: Scheduled and planned maintenance on equipment when it is not in use. Typically based on predicted or measured failure rates and history.
4. Training and Education: Operators are trained and educated in simpler AM tasks, Maintenance employees are trained in proactively and preventively performing maintenance tasks, managers are trained in TPM and coaching of employees
5. Early Management: Helps engineers and others choose and buy the right equipment with the gained knowledge about equipment, processes and TPM. An example could be that a maintenance technician notice that the belt of a machine is located in a shut-off location in the machine, but gained experience says that the belt wears out every three months. To change the belt, it would perhaps take half a day but if they change the design and implement a lid it can be done in half an hour
6. Quality Maintenance: Designing error detections and prevention as Poka Yoke into the production processes as well as applying Root Cause Analysis to prevent recurring sources of quality defects
7. Office Kaizen: This means applying the TPM methodology in the office environment by supporting the production processes and removing wastes in the administrative processes, for example by providing spare parts or materials
8. Safety, Health and Environment: Maintaining a safe, healthy working environment
So, as you probably see, the TPM is not something that should be taken lightly and not something you implement in a short time. But that does not mean you cannot get started quickly and realize good results fast.
Equipment Kaizen on a stand-alone automatic assembly machine
And that is exactly what I will touch upon in the case that I want to tell you about. We were about to make a pilot on TPM and chose to run the pilot as a Kaizen Event. Shortly explained, a Kaizen event is a very structured way to implement improvements fast in about 5 days. The focus is on execution and getting results through a very intensive process.
The machine was a stand-alone automatic assembly machine that makes electrical outlet sockets.
Before the Kaizen Event
Before the actual 5 days event, we went on the Gemba (you ALWAYS find the truth on the Gemba), where we made videos on how the equipment was performing. We filmed how the parts were grabbed in the jigs, how screws were put in premade holes by a screwdriver, how the part moved around in the machine etc. After that, we went into the red bins (bins with bad parts located by the production line) that is, the bins were almost empty so we had to dive into a larger container to fetch different bad parts.
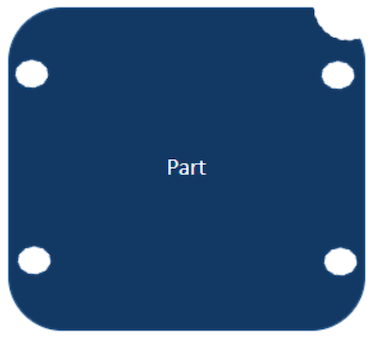
And there was different kind of quality issues but especially one defect appeared quite a lot. It was parts with a dent in one corner. That seemed odd. So, we went back to the Gemba and observed how the parts were held in the jigs. We watched for some time and then agreed on the hypothesis that the dent was created in a certain spot in the machine. We then went back to watch the videos and with the help of the slow-motion functionality, we could see that one of the arms of the jigs pressed more on one side than the others. This did not happen every time but we were pretty sure now that we had attained the root cause of the dent.
Watching the machine and the videos closely we discovered something else: the screwdriver was placed about 20 cm above the screw that it was supposed to drive in despite the fact that the piece would never be that tall. We later found out that the machine had been previously running another taller piece but was now running a much smaller piece. We made a small experiment moving the screwdriver down making sure that it would not collide with anything on the plate. This would reduce the cycle time considerably.

Screw Driver moved down 10 cm to reduce cycle time. Image provided by Erik T. Hansen
Moreover, we noted small quick fixes made with string or duct tape etc. that would be replaced during the event. So, we made sure that those parts etc. were ordered so that they would be in stock at the time of the event.
We now had a catalogue of possible improvements that we could work on when we were running the Kaizen event. And needless to say, we were looking very much forward to the event.
The Kaizen Event
Then it was time for the event, and of course, everybody was introduced to the work at hand. The first day is normally spent washing and cleaning the equipment. That means that everybody cleans the machine, including leaders and Lean professionals. So, we washed down the machine, cleaned windows and screens etc. Everything was cleaned and later the machine almost looked new. Clean windows, all oil stains and dirt were washed away and everybody were pretty proud of the good job they had done. During the cleaning, everything that was out of order or standard was noted on an activity list.
The next day we split into two groups, operators and maintenance technicians:
The operators sat down with a maintenance technician and identified the daily lighter and simpler maintenance tasks that could be done by the operator. After identifying the so-called Autonomous Maintenance tasks Standard Operating Procedures (SOPs) were written and the operators were trained in performing the tasks. This included implementing visual management gauges to make sure that the operator easily could see if the oil level was at the right level and that the speed of the equipment was in the correct position. This was implemented using red-yellow-green indicators. The group worked on that the rest of the week.

The maintenance group went through the spare part list and made sure that all parts that were necessary were in stock or would be ordered. Then we went on to the improvement catalogue and the screwdriver was moved down 10 cm and it worked like a charm reducing the cycle time considerably. We investigated the problem with the dent and found out that one of the arms was tightened too much so that the jaw pressed the piece and, in that way, made a dent in the part.
After the Kaizen event, everybody were happy they participated and acknowledged both the strength of Kaizen Events and TPM. The result from the Equipment Kaizen was that the OEE was improved from 47% to 70% and that is (of course) counting the new lower cycle time.
A word of warning: when you start this kind of event make sure you mean it and get everyone involved and if you reduce the cycle time, do not cheat: remember to measure the new performance with the new cycle time. Otherwise, you will have a very good increase in OEE but it will not be a real improvement.
As you can see from this case we worked with and implemented quite a few of the pillars in the TPM methodology and created a well-performing machine.
Links
I provide you with some links if you should be interested in reading more or follow me.
LinkedIn: https://linkedin.com/in/erikthansen
Blog: https://etorreshansen.wixsite.com/thoughtsfromthegemba